Jetzt oder nie: Volker baut eine CNC-Fräse
Kein von Hand geführtes Werkzeug ist so präzise, und viele hätten daher gern eine, um sich damit Maßanfertigungen aus Holz oder Metall zu machen: eine CNC-Fräse. Volker hat sich eine gebaut. In einem Workshop – denn ohne professionelle Hilfe geht das kaum.
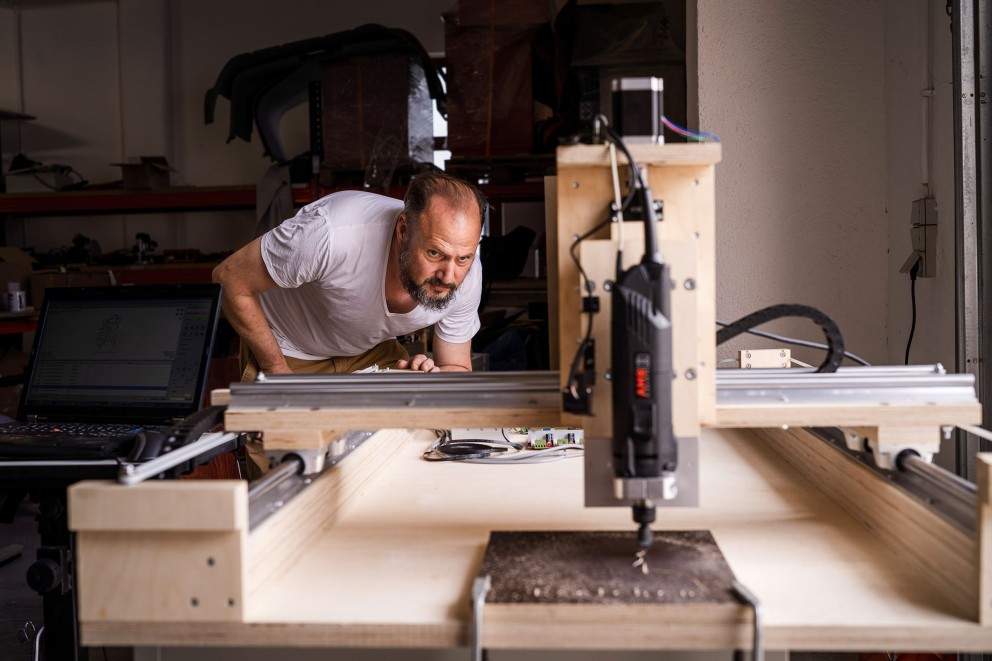