Meisterwerk: Der HORNBASS
Einen E-Bass spielen, den man selbst gebaut hat. Mit Materialien aus dem Baumarkt. Das ist Mikes Projekt.
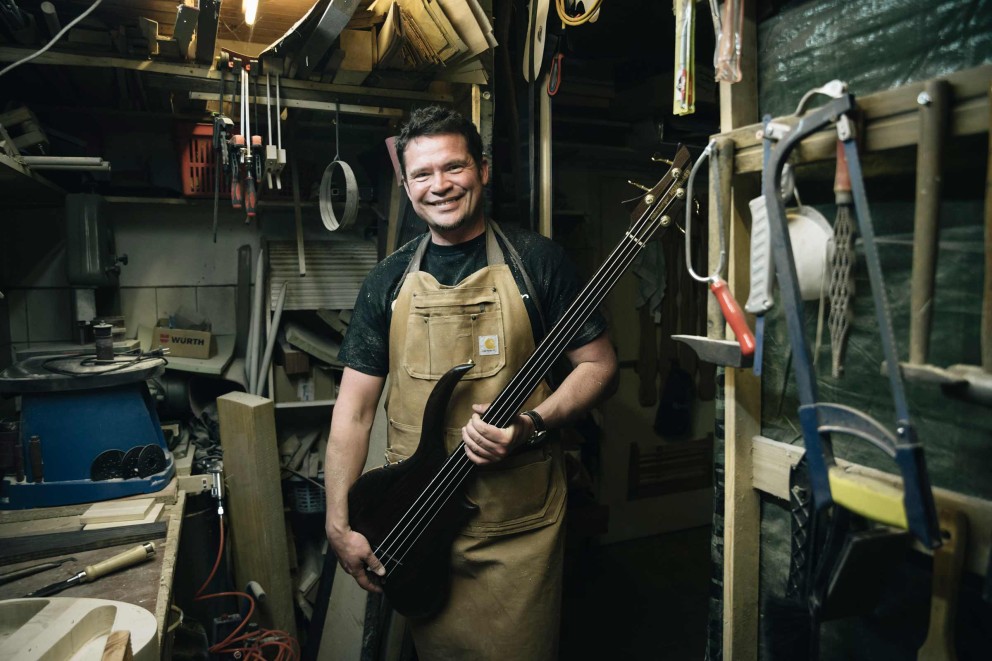
Mike Bolz‘ Leidenschaft: Mit Holz arbeiten – und abrocken. Am liebsten am E-Bass. Wie der Bassist von Metallica. Die Idee: Beide Leidenschaften verbinden. Einen eigenen E-Bass bauen. Gesagt, getan? Nicht ganz. Theoretisch war es einfach, praktisch nicht. Einen günstigen Bass komplett zerlegen, viele Gitarrenbauer nerven. Immer wieder fragen: „Wie geht das? Wie macht man das?“
Mike ließ sich nicht abbringen. Auch nicht durch Fehlversuche. Endlich fertig, sein erster E-Bass. Das war vor 30 Jahren.
Rund dreißig Gitarren und E-Bässe später – selbst gebaut, umgebaut, saniert. Äußerlich ist Mike ruhiger, gediegener. Arbeitet als Architekt und Bauleiter. Innerlich noch immer der alte Rocker. Und sucht stets nach dem nächsten Bauprojekt: ungewöhnlich. Verrückt. Anders. Hauptsache mit Holz.
Dieses Mal will er weiter gehen. Allen beweisen: Man muss keine außergewöhnlichen Materialen verwenden, um einen schönen E-Bass herzustellen. Der dann auch noch super klingt. Mit Material vom Baumarkt geht’s bestimmt auch. Kann sich jeder kaufen. Denkt sich Mike. Tigert durch die Gänge, stößt auf Terrassendielen. Aus Esche, Bambus, Douglasie. Thermo-Hölzer, bestens geeignet für den Instrumentenbau. Die richtige Feuchtigkeit, extrem wenig Harze. Das Gewicht für den Bau eines leichten Instruments passt auch. Sollte funktionieren, entscheidet Mike. Schreitet mit drei Dielen als Probekauf zur Kasse – und zur Tat.
Er entwirft etliche Skizzen, verwirft sie wieder. Endlich passt es, und er baut Schablonen aus Sperrholz für Korpus und Hals. Sägt die Einzelteile grob aus, baut den Korpus: leimt Boden- und Deckenhölzer – aus heller Douglasie und dunkler Thermo-Esche – zusammen. Schneidet den Korpus großzügig aus, fräst Rundungen. Passt. Fehlt noch ein Fach für die Elektronik, wieder geht’s an die Fräse. Dann ist der Hals dran. Ziemlich kompliziert: neun Holzschichten – Thermo-Esche und Thermo-Bambus mit ein paar dünnen Furnierstreifen Ahorn für zusätzliche Stabilität dazwischen – auf die richtige Stärke sägen, hobeln, zusammenleimen. Per Hand die idealen Rundungen und Radien des Halses ausarbeiten. Die Form der Kopfplatte festlegen und fräsen. Eine Heidenarbeit. Trotzdem: Weitermachen! Korpushälften mit dem Hals verleimen, Halsstab einfräsen.
Nächster Schritt: Das Bambus-Griffbrett auf den Hals leimen. Fehlt noch die Technik: Stimmmechaniken, Tonabnehmer und Saitenhalter in den Korpus einbauen. Und die ganze Elektronik verlöten. Klingt so einfach. Dauert aber lange: Mike probiert fünf Elektroniken, zehn Tonabnehmer aus. Klingt nicht. Nicht für Mike, den Perfektionisten. Er hat eine genaue Vorstellung davon, wie der Bass klingen soll. Entscheidet: Er baut die Saitenhalter am Korpus aus Messing selbst, die erzeugten den richtigen Druck auf den Piezo-Tonabnehmer. Auch Teile der Elektronik entstehen in Eigenregie: Er schmeißt Bauteile aus Elektroniken raus, lötet andere Komponenten ein. Endlich ist er da, sein Wunschsound: wohlig warm, schnurrend, wie ein toller, bundloser Bass klingen soll. Zum Schluss der Feinschliff mit mehrfacher Ölung und Politur. Passt.
Nach drei Monaten Arbeit: Mikes erstes Mal am „Hornbass“. Der Sound haut ihn um. So hat Mike sich das vorgestellt. Ein Klang mit lang-anhaltendem Ton, durchsetzungsstark. Perfekt, vor allem für Rockklassiker der 80er und 90er. Rocker bleibt halt Rocker. Auch ohne lange Haare.
Text: Esther Acason | Fotos: Roman Pawlowski